1、引言
钛合金被广泛应用于各个领域,提高钛合金切削性能,使其加工成本更低,并开发出性能更好的新型钛合金是钛合金加工的主要研究方向。钛合金三种基体组织——α合金、(α+β)合金和β合金,我国分别以TA、TC和TB表示,其中TC4钛合金最受青睐。国内外学者对钛合金开展了大量研究工作,其中以对TC4钛合金的研究居多。
2、钛合金切削工艺研究进展
2.1 切削参数优化
优化切削参数对于提高生产效率和改善表面质量等有着至关重要的影响,国内外学者对此进行了大量研究。胡伟楠[1]对TC4高速切削的不同切削参数组合进行了研究,发现在切削速度v=72.2~101m/min,切削深度Ap=0.5mm,进给量F=0.11mm/r时,TC4钛合金的切削加工性能较为理想,且加工表面质量优于低速范围。郭涛[2]通过制定新的TC17零件车铣复合加工工艺路线,并用车削试验优化切削参数,设计了将加工效率提升三倍的夹具。孙程成[3]根据枪钻的全因素实验结果选取了最优加工参数,制定了TC4舵骨架零件高精度深孔的加工工艺方案,但测量值在技术要求范围的边缘,需要进一步改进。续文浩[4]提出了基于叶片
型面余量分布的变进给优化方法,并优化了叶片型面粗铣加工的进给参数。王胜等[5]采用逐步增大切削参数的方法对双刃PCD刀具铣削TC4钛合金进行了工艺优化,获得了令PCD铣刀耐用度与寿命较长、工件表面质量与形貌较好的工艺参数。
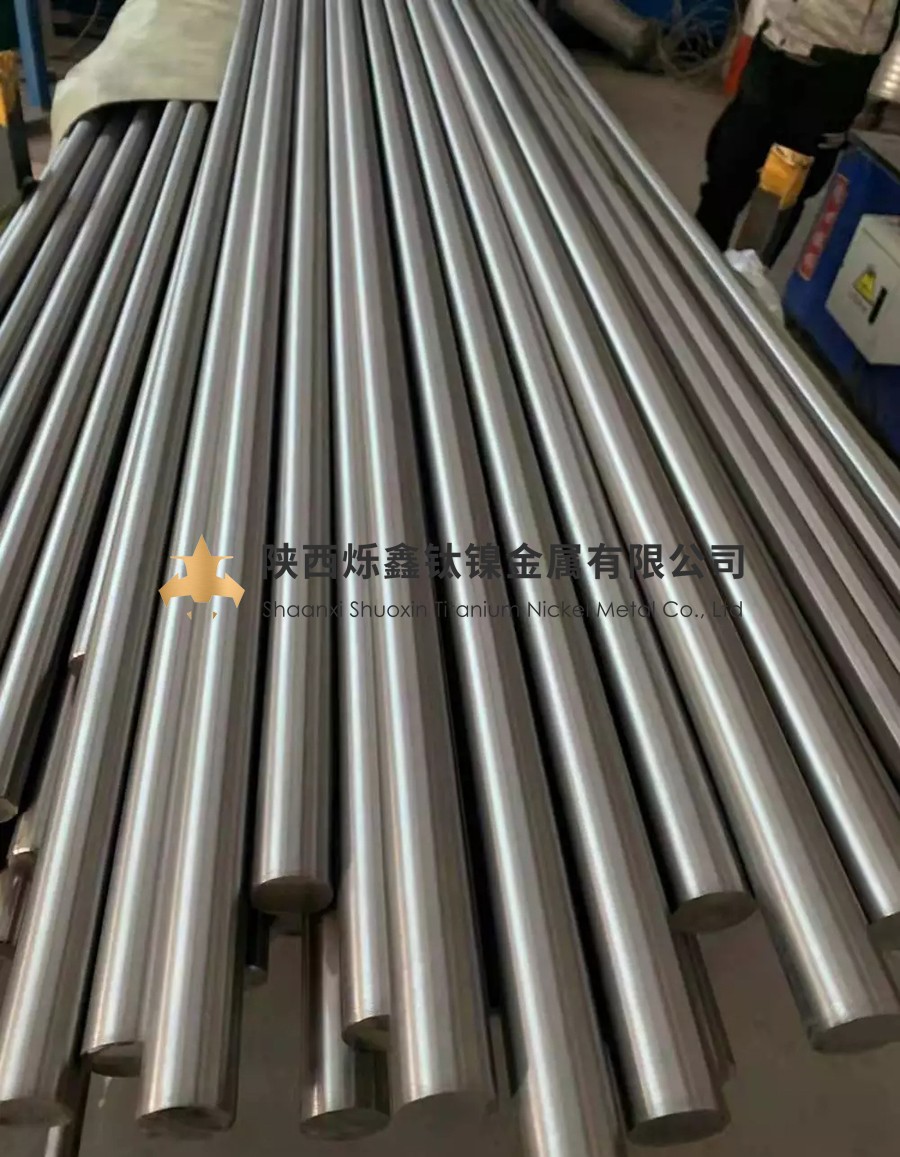
杜红春等[6]采用量子粒子群算法对传统的Kriging变异函数参数进行优化,将误差从(-20,10)缩小到(-15,10),得到了精度较高的数学模型。赵云琨[7]以低残余应力为目标,将最大压应力、最大压应力层、最大拉应力和最大拉应力层作为目标函数,利用评价函数法对其进行了优化。SuiShAoChun等[8]采用响应面法解释了铣削温度随加工参数的变化规律,建立了相应的数学模型并验证了其显著性。
将田口法与灰色关联度理论相结合,可对TB17钛合金的疲劳性能及表面完整性进行优化分析,但不足之处是计算灰色关联度时未考虑权重系数且测量因素不够全面[9,10]。W.merSni等[11]采用球头立铣刀铣削倾斜角度为25°的TC4工件,未获得最佳的三维平均表面粗糙度,采用田口法对工艺参数进行了优化,利用信噪比分析得出的表面粗糙度最优水平,并用实验验证了其有效性。
在遗传算法的应用方面,刘杨[12]利用遗传算法基本原理构建参数优化模型,并使用mATLAB软件进行了多目标参数优化,但被研究对象局限性较大且通用性较差。此外,采用nSGA⁃ii遗传算法进行多目标优化也是一种可行方法[13],陆涛[14]在有限元模拟仿真的基础上,采用mATLAB遗传算法工具箱进行参数优化,但是其建模过程中忽略了刀齿数和刀具角度等因素的影响,模型的通用性有所欠缺。
在钛合金薄壁件加工研究方面,陈国三[15]通过研究各因素对加工变形的影响程度获得了令变形最小的参数组合。陈虹宇[16]绘制了薄壁件铣削过程中关于铣削参数的三维稳定性图,并通过正交实验法进行验证,得到了最优加工参数。陈婷婷[17]以提高切削瞬时区域刚度为目标进行了刚度优化试验,最终加工出厚度差值不到0.06mm、弯扭变形不到0.1mm的钛合金薄壁腹板。章熠鑫[18]从减小切削力和增大工艺系统刚度两方面对薄壁件加工进行了优化,但其建立的切削力预测模型无法对不同工件结构及不同刀具进行准确预测。
鲁炎鑫[19]的研究结果表明,当刀具未开始磨损时,其对工件表面z方向粗糙度的影响程度排序为切削速度>每齿进给量>铣削宽度>铣削深度;当刀具后刀面磨损宽度VB=0.05mm时,对工件表面z方向粗糙度的影响排序变为切削速度>铣削宽度>铣削深度>每齿进给量。罗秋生等[20]的研究表明,冷塑性变形引起的残余压应力在高速铣削TC17钛合金中占主导地位,同时以低应力为目标得到了最优的铣削参数。V.KriShnArAj等[21]研究发现,切削深度和进给速度对切削力影响最大,而切削速度对温度影响最大,并给出了所研究的加工范围内适合高速加工的参数。Luoming等[22]的研究表明,每齿进给量和径向切削深度对刀具磨损有很大影响。
为了减少刀具磨损,推荐切削参数为每齿进给量FT≤0.07mm/z,径向切削深度Ae≤1.0mm,轴向切削深度Ap≤2.0mm,切削速度可设置为60~150m/min。mAJiAnwei等[23]研究表明,钛合金曲面高速铣削的切削力与曲面几何特征及主轴转速有关,为了使切削力最小,在主轴转速2000~23000r/min范围内进行实验研究,得到主轴转速的最佳范围是9000~13000r/min。
2.2 加工表面完整性
加工过程造成的零件表面缺陷往往是零件破坏的源头,因此各国学者越来越重视针对表面完整性的研究。
ThomASmeurig等[24]提出,目前对表面完整性的研究主要集中于宏观特征层面,但对高速铣削过程中产生的亚表面微观组织损伤鲜有关注。为此,张一鸣[25]选取表面粗糙度等5个参数作为评价指标,以TA11和TC4钛合金为试验对象,从单一加工方式入手,得出了多工序连续加工对各评价指标的影响规律。而杜舜尧[9]则选择了表面粗糙度、表面加工硬化、表面残余应力及表面形貌作为评价指标,以新型TB17钛合金为试验对象进行了研究。在多工步连续加工方面,侯冠明[26]对钛合金进行了两工步和三工步车削加工,分别选择粗加工切削参数和半精加工切削参数为变量,得出了下一工步表面完整性受上一工步参数变化的影响规律。
在对表面残余应力的研究中,孟龙晖[27]研究认为,对最表层残余应力分布影响最大的是切削温度,对次表层残余应力分布影响最大的是切削力,但是没有对材料的相变做进一步研究。增大刀尖圆角半径和刀具前角会令表层残余压应力大幅度减小,升高工件预热温度也会令工件次表面残余压应力减小[28],降低每齿进给量和铣削速度、提高铣削深度都会令表面残余压应力变大[20]。TC4钛合金表层最大压应力出现在深度约0.05mm处,深层最大拉应力出现在深度约0.3mm处,随着切削速度变化,残余应力层的深度分布无明显变化[29]。YAngDong等[30]提出了一种将有限元方法与统计模型相结合的混合方法,在有限元模拟的基础上采用粒子群优化方法拟合指数阻尼余弦函数,研究了表面残余应力、压应力峰值、位置和响应深度四个因素对切削速度和进给速度的影响,随着切削速度和进给量的增加,残余应力由压应力向拉应力转变,压应力峰值减小,位置和响应深度增大。XinHongmin等[31]发现残余压应力随主轴转速的增大而减小,但随切削深度和进给速度的增大而增大;随着切削深度增加,残余压应力逐渐转化为拉应力并最终消失。
在表面粗糙度方面,有研究表明,颤振表面的粗糙度值是平稳表面的四倍以上,为了尽量降低或消除颤振,建议采用多齿数、大刀径、高转速及小进给的加工策略[32],但该研究的缺点是对表面质量研究时所选的指标不够全面。赵伟静[33]通过单因素试验研究了不同范围的砂轮线速度和进给速度对表面粗糙度值的影响规律。李军等[34]和王晓明等[35]研究发现,对表面粗糙的的影响程度为铣削宽度>每齿进给>铣削速度>铣削深度,且显微硬度的最大值出现在已加工表面的表层,其数值比基体增加了
13%~50%,最小值出现在表面层深度20μm处。
而V.KriShnArAj等[21]的实验结果表明,进给量对表面粗糙度的影响较小,原因可能是所用刀片具有雨刷几何形状。周子同等[36]进行TB6钛合金铣削试验发现,v线<40m/min或v线>100m/min时粗糙度值较低,又因为进给量是影响粗糙度的主要因素,因此在此范围内选取线速度以及较低的进给量可以获得较低的表面粗糙度值。W.merSni等[11]研究表明,对表面粗糙度影响程度的大小是径向切削深度>切削速度>每齿进给量。另有研究认为切削速度对表面粗糙度有明显影响,分析可能是由于齿槽铣削过程中刀片的擦拭作用导致[37]。
为了探究刀具几何参数和工艺参数对表面完整性的影响,宋绪浩[38]研究了工艺参数对TC4加工表面质量的影响规律及微观机理。通过对典型钛合金TC1、TC4和TA5进行对比实验得出,切削深度是对钛合金加工表面质量影响最小的因素,想要获得7级以上的表面光洁度,推荐在进给量F≤0.16mm/r、刀具磨损量VB≤0.3mm的条件下进行加工[39]。孙明杰[40]分别对不同退火方式的TB6和TC4钛合金的铣削加工工艺进行研究,得出了铣削参数对各表面完整性评价指标的影响规律。在TC17铣削过程中,刀具取向对表面形貌、残余应力和表面粗糙度影响较大,但对显微硬度影响较小,当旋转角度为0°~90°、倾角为30°~60°时,表面完整性最佳[41]。LiYu等[42]对TC17钛合金进行了相似研究,结果表明,铣削速度、每齿进给量和铣削深度对表面组织的影响较小,且未产生明显相变。李锋等[43]通过进行TC11铣削试验得出,要想得到较小的表面粗糙度和残余应力,刀具磨损应避免进入剧烈磨损阶段,即磨损量不应超过0.3mm。杨后川等[44]研究认为,精加工TB6钛合金时刀具磨损量小于0.2mm的条件下表面完整性较好。
2.3 润滑冷却
选择合理的润滑冷却方式可以起到降低切削力和切削温度,以及延长刀具寿命的作用,尤其对于钛合金材料,可以起到改善切削性能的作用。一般孔径的TC4钛合金材料,深孔钻削加工系统和刀具选用普通乳化液即可起到很好的冷却及润滑作用[45]。杨晓勇[13]研究发现,在一定的铣削速度范围内,干切削与使用乳化液切削得到的表面完整性非常相近。SurojiTGAnguli等[46]对钛合金在应用不同切削液应用下的切削性能进行了比较,ACF喷雾系统可使刀具后刀面磨损均匀,降低切削力,提
高表面光洁度,且刀具寿命比溢流冷却条件下的提高达75%,形成的切屑比溢流冷却更短、更薄。
nAoToiShii等[47]利用可选光纤的双色高温计测量刀具边缘温度,提出了基于刀具边缘温度测量的切削液评价方法。黄丙琪[48]提出了通过热/冷复合切削钛合金的方法,研究了超声雾化水基切削液、超声雾化moS2切削液、mQL水基切削液与25W、50W功率的激光分别进行复合切削,并将刀具磨损程度与单独的冷
效应方法和激光加热法进行了比较,但是该研究主要在中低速条件下进行切削试验,其结论不一定适用于高速切削。
Kyung⁃HeePArk等[49]还采用了一种新型微量润滑技术,即在润滑剂中加入少量(~0.1%)脱落石墨纳米片(xGnPS),与其他技术的对比结果表明,低温加工和mQL均优于干湿加工,但mQL与纳米颗粒相结合(mQLn)加工的PV比(峰谷比)最低。Kyung⁃HeePArk等[50]的研究还表明,在TC4钛合金的深轴向切削深度加工中,向增强的mQL中添加hBn纳米颗粒并结合内部低温冷却,结果比传统驱油冷却条件下的刀具寿命提高了32%。
2.4 切屑研究
在切削过程中如果断屑出现问题容易造成刀具损坏,降低加工表面质量,甚至影响机床正常工作和操作人员的安全。
普通铣削的切屑表面非常粗糙并具有大量连续带状条纹,且存在严重塑性变形,高速超声椭圆振动铣削的切屑呈针状,宽度明显窄于普通铣削切屑,切屑表面较为光滑,纹理分布均匀,其塑性变形也明显较小[51,52]。邵振宇等[53]使用八面钻结合超声振动钻削技术进行了无冷却条件实验,发现产生的切屑比普通钻削的切屑短很多。
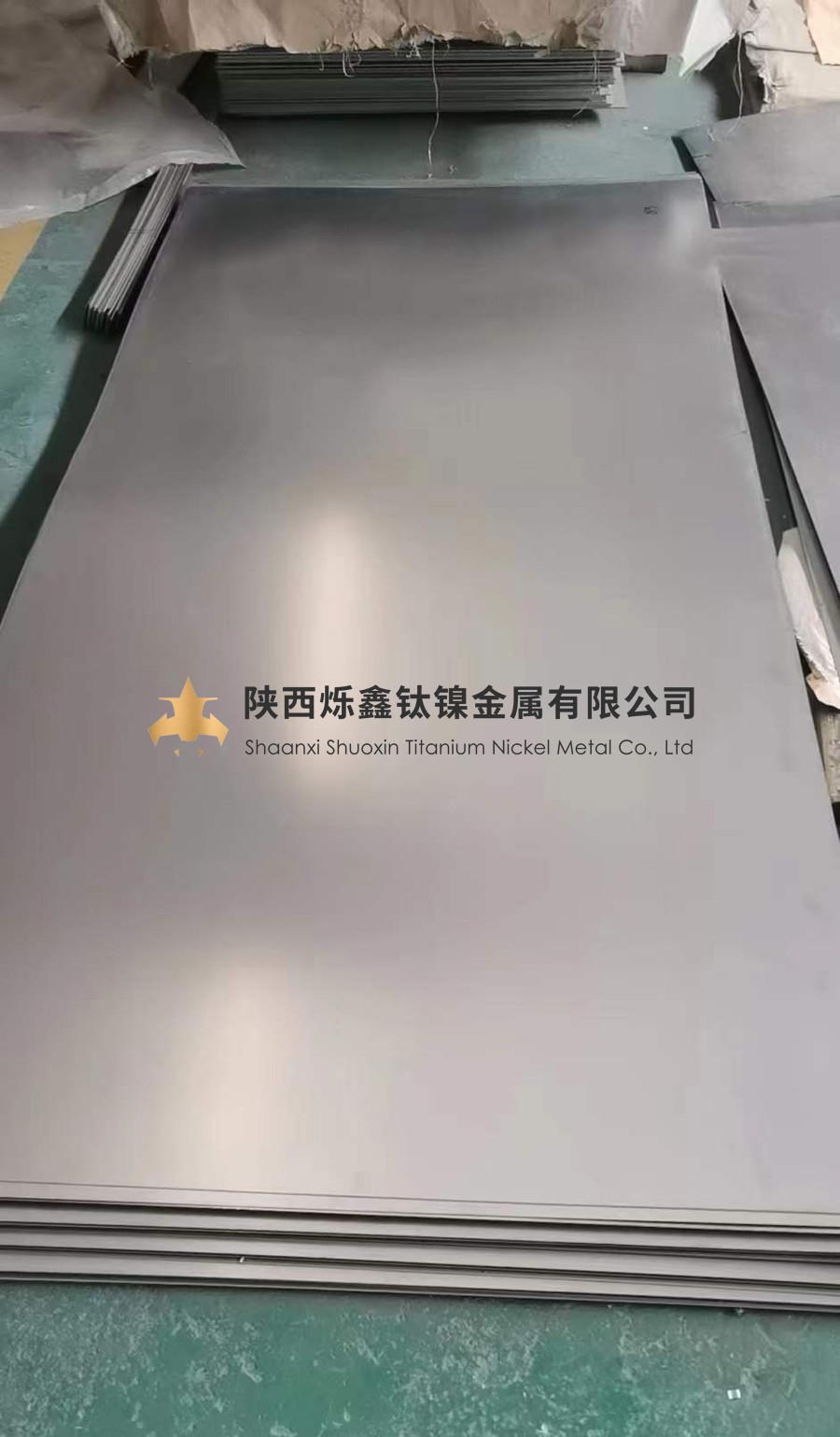
高速铣削实验结果表明,影响切屑形态最主要的因素是切削速度,增大切削速度会使得切屑形状更为规则,毛边数量下降,裂纹减少,背面划痕消失,且单元尺寸增大[54,55]。高速切削条件下,切屑的锯齿化程度与切削深度和刀具前角成反比,与切削速度成正比;而进给量对锯齿形状的影响不明显[29],因此可以通过选择适当的刀具前角来控制切屑形状。王来照等[56]通过对TC4钛合金进行高速干铣削单因素加工试验发现,随着铣削速度、每转进给量和轴向切削深度的增加,锯齿的间距齿宽和齿高越
来越大,切屑锯齿化程度逐渐增加。
孟龙[28]通过系统分析各因素对切屑形态的影响得出,在一定范围内,随着刀具转速与进给量的增大,切屑锯齿的数量呈上升趋势,刀具前角与切屑卷曲程度成正比,而刀尖圆角半径对切屑的影响较小。LiAnhAi等[57]通过PCD刀具高速铣削TC4钛合金实验发现,随着切削速度的增加(125~2000m/min),切屑的变化规律为长直线型→螺旋形→卷曲形→不规则形,且观察到切屑的自由表面呈锯齿状片层结构,切削速度越快,薄层越清晰明显。
2.5 切削工艺发展趋势
2.5.1 超声振动切削
超声振动辅助切削是通过将刀具与工件进行周期性分离来辅助加工的一种加工方式,具有切削力小、加工精度高、切削温度低和切削表面粗糙度低等优点,是一种革命性的加工工艺。2017年3月,焦峰等[58]提出将超声振动和高速加工技术有效复合来获取更高的加工效率。同年10月,高速超声振动切削的概念被张翔宇等正式提出[59],其切削力与普通切削相比减少了20%~50%,且刀具寿命提高了1.5~3.0倍,并可以在长时间加工过程中将表面粗糙度保持在0.4μm以下。
2021年,该团队通过分析运动轨迹与运动方程,计算得出超声振动切削的进给量需要小于两倍刀具振幅,且相位差距离π越近,分离效果越好[60]。在高速超声振动切削的基础上,LiuJiAjiA等[61]提出了一种高速旋转超声椭圆振动辅助铣削加工方法,该方法可以显著提高切削效率,减少更换刀具的时间。
倪陈兵等[52]研究表明,随着振动振幅的增加,x和y方向的切削力最多可降低60%。邵振宇等[53]使用八面钻结合超声振动钻削技术、在无冷却条件下进行钻削试验发现,钻削力比普通钻削降低了20%左右,扭矩降低了31.66%~34.3%。在TC4薄壁件超声振动辅助立铣削过程中,各因素对误差的影响程度为轴向切削深度>超声振幅>每齿进给速度>径向切削深度>切削速度[62]。
2.5.2 微切削
如今,医疗组件和通信信息设备逐渐向小型化和轻量化方向发展,又由于钛被广泛地用作这类设备的零件材料,对钛零件进行必要的微加工和铣削便成为了当下的主要研究方向。
王瑛[63]研究发现,微切削中切削速度对磨损量的影响比切削深度大,且增大切削深度(0.1~0.5mm)会使得刀具寿命减少一半,但加工效率提高约4倍。KojiTSudA等[64]使用直径小于1mm的方形微型立铣刀进行实验,结果表明,当干切削的切削速度从50m/min增至200m/min时,表面粗糙度的大小差别不大,可以进行高速切削,切削液在微型立铣刀铣削时有抑制凝集作用,刀具不会产生热裂纹。
3、钛合金切削刀具研究现状
对于钛合金这种难加工材料,其性能决定了对切削加工的要求极高,这也使得刀具选择、刀具几何参数优化以及开发新刀具变得尤为重要。
3.1 刀具结构的研究现状
3.1.1 刀具几何参数
杨东[65]研究了刀具前角与刀具刃口钝圆半径等因素对切削方向和切削宽度方向残余应力的影响规律,且与文献[29]所得的规律基本相同。张建飞[66]利用遗传算法多目标优化程序优化了刀具几何参数,但是只考虑了刀具前角、后角和钝圆半径三个参数,不够全面。RenJunxue等[67]使用与田口法相结合的灰色关系分析,将多目标优化转化为灰色关联等级的单一目标优化,对BT22钛合金末端铣削进行了刀具几何参数优化。
徐九华等[68]认为PCD刀具整个刀刃失效的原因是刀具前角和后角过大,刀具强度不够而导致严重崩刃,经过改进刀具几何参数,在相同条件下对退火后的TA15钛合金切削30min,切削刃不再出现崩刃现象。BAiJinxuAn等[69]对刀具几何参数进行优化后,使用该PCD刀具切削TC4钛合金的表面粗糙度RA=75nm,优于大多研究值。
3.1.2 刀具磨损
在刀具磨损形式方面,整体硬质合金立铣刀铣削TC4钛合金时,刀具前刀面发生氧化磨损和黏结磨损,产生机械裂纹和热裂纹,不同的是后刀面没有热裂纹产生[70]。PCD刀具的主要磨损特征为刀尖磨损、后刀面磨损和前刀面磨损,且较小刀具钝圆半径以及较大前角和后角有利于减少缺陷数量和亚表面损伤层厚度[69]。罗学全等[71]探究了PVD涂层刀具在TC4高速铣削加工中的磨损形式,发现刀具的前后刀面都以黏结磨损为主,而刀具的刃口以黏结磨损和热—机械疲劳磨损为主。
在刀具磨损影响因素的研究中,何耿煌等[39]研究发现,刀具磨损是导致表面硬化最主要的因素,若磨损量从0.2mm增加到原来的3倍,则其表面硬化程度也将会增加到原来的3倍。此外,每齿进给量和径向切削深度对刀具磨损影响较大,轴向切削深度和切削速度对刀具磨损影响较小[22]。微织构球头铣刀铣削钛合金时,前刀面和刀屑接触区域极易发热和磨损,而刀尖处温度受影响较小,刀具表面的温度分布较为均匀[72]。王瑛[63]通过理论计算表明,Co元素是引起硬质合金刀具在加工过程中发生扩散磨损的主要元素。
由于现有刀具磨损评价方法并不能适用于所有切削情况,闵令臣[73]通过观察锐利刀具切削钛合金时的刃口磨损过程,提出了基于刃口钝圆磨损的刀具磨损评价方法。在刀具选择上,ShiQi等[74]对TC21钛合金的切削性能进行了多项试验研究,对刀具寿命的分析得出,WK10的刀具寿命足够长,磨损形式相对良好,是目前更适合加工TC21钛合金的刀具。
3.2 新型刀具
3.2.1 表面织构刀具/微织构刀具
苏永生[75]分别使用YG8微沟槽刀具和PCD微沟槽刀具在干切削和低温微量润滑条件下进行试验,分析了微沟槽刀具改善摩擦状况的作用机理。
3.2.2 涂层刀具
胡伟楠[1]通过实验发现,PVD涂层硬质合金刀具高速切削TC4钛合金的性能比CBn立方氮化硼刀具更好。罗胜[76]对六种硬质合金刀片进行了性能更好,且抛光PVD刀片的耐用度要优于磨削刀片。WilmAPolini等[77]采用三种涂层硬质合金立铣刀进行TC4钛合金加工试验,其中单层TiAln刀具比多层TiAl和多层TiAln涂层刀具的切削力更小,寿命更长,平均表面粗糙度相对最小。切削速度为200m/min时,TiAln、TiCn、DLC涂层硬质合金刀具
和未涂层硬质合金刀具在磨损过程中的刀具寿命表现为未涂层刀具<TiAln涂层刀具<DLC涂层刀具<TiCn涂层刀具,其中,TiAln涂层刀具的油雾切削
寿命是干切削寿命的1.6倍[78]。在对VT20钛合金的铣削研究发现,Zr⁃Zrn⁃(Zr,Cr,Al)n涂层刀具比Ti⁃Tin⁃(Ti,Cr,Al)n涂层刀具寿命更长,这是由于涂层Zr⁃Zrn⁃(Zr,Cr,Al)n使刀具抗裂纹形成和脆性断裂能力显著提高[79]。在相同切削条件下,PCD刀具高速铣削TA15钛合金时,刀具寿命明显优于PCBn刀具,PCD刀片在加工过程中产生的平均表面粗糙度低于PCBn刀片[80]。
林凤添[81]通过添加TAC(nBC)制备了新的硬质合金刀具,在800℃时,该刀具的硬度比未添加TAC(nBC)时提高约14.5%,断裂韧性提高约
10.2%,且刀具磨损更轻微,刀具寿命更长。mATThewS.DArguSCh等[82]对四种硬质合金涂层刀具在两种不同速度下进行了激光辅助加工(LAm)测试,发现现有的刀具涂层不能完全解决磨损问题,因此认为LAm领域的工作应集中于开发新一代刀具以及刀具冷却策略。
3.2.3 仿生刀具
姜振喜[70]通过观察玉米叶子边缘齿形,设计了具有特殊槽型和微刃结构的立铣刀,与普通立铣刀相比,仿生刀具的切削振动和切削温度更低。但是刀具结构的匹配关系以及刀具耐用度等方面的研究尚不全面。
4、钛合金切削仿真技术研究现状
由于计算机技术的快速发展,有限元仿真的应用开始普及,精确性也逐渐提高,对降低试验成本和提高生产效率起到重要作用。
唐柏清[83]建立了硬质合金刀具切削钛合金的磨损仿真模型,随着时间增加,前刀面磨损的仿真值与实验值的变化趋势越来越吻合。孙玉晶等[84]在构建类似模型后,利用AdvAnTEdge的二次开发技术,将其嵌入有限元模型中,对材料失效模型进行了分析。张富君[85]将切屑成形过程仿真与刀具磨损率数学模型相关联,形成刀具磨损仿真系统,确定了刀具磨损仿真路线。钱丽丽[86]基于ABAQUS软件进行二次开发,将不同功能集成到有限元仿真平台上,实现了加工过程的快速仿真。
杨东[65]将有限元模型与残余应力轮廓函数模型相结合,建立了残余应力预测综合模型,但是其研究存在一定的假设条件,对实际加工参数进行了转换,在数值上存在偏差。孟龙[28]建立的TC4高速铣削二维有限元模型,在铣削力、铣屑形态和铣削表面残余应力三个方面的误差皆不超过21.4%。在模拟切削参数对残余应力分布影响的过程中,如果想要得到较大的工件表层残余压应力,推荐选择较小刀具前角、较大刀具后角和较大刃口半径[29]。
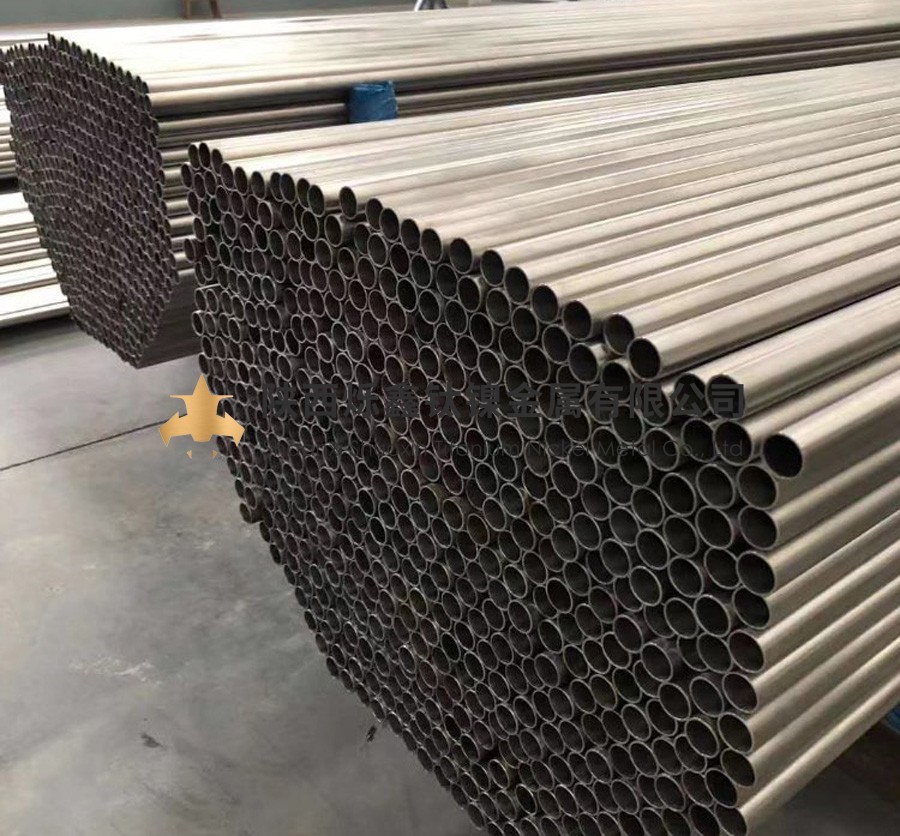
周培培[87]模拟了高速车削TC4与TA15钛合金过程,发现切削力跟锯齿形切屑的变化趋势十分接近,切削力随着切屑的形成迅速减小。HuAngShuTAo等[88]在钛合金大切削深度准高速铣削模型的基础上,研究了切削温度和切削力随切削参数变化的规律,其中最大切削温度出现在刀尖圆弧型面的切削刃处(800℃左右)。
在三维切削仿真研究方面,孟龙晖[27]将正交切削仿真和正交压痕仿真相结合,代替了三维切削仿真。陈国三[15]通过建立高速切削三维有限元模型,对切屑的形成过程进行了仿真,发现最大应力值和最大切削温度分别出现在第Ⅰ变形区和第Ⅱ变形区,仅对模型底部进行完全约束,未考虑夹紧及夹具的定位对加工变形的影响。陈婷婷[17]建立了变刚度三维仿真模型和热力耦合三维动态铣削模型,并将误差控制在0.0681mm和0.0255mm内,但是为减小计算量,两种模型均是简化模型。LinYouxi等[89]建立了高速铣削TC4钛合金的三维全热—力耦合有限元模型,对铣削温度进行模拟分析结果表明,铣削热只影响被加工表面层的温度,刀具温度随铣削速度和径向切削深度的增加而升高且影响小于切削速度。WAngZhendA等[90]在TC4钛合金三维铣削有限元仿真模型的基础上研究得出切削参数对铣削力的影响程度为轴向切削深度>刀具速度>进给速度。
王瑛[63]通过建立斜切模型,对最小切削厚度进行了仿真计算,降低了切削厚度的设置误差导致的最终仿真误差。武永甫[91]考虑刀具的旋转和进给运动,通过建立二维变厚度连续铣削仿真模型,实现了连续铣削的数值模拟。
5、预测模型研究现状
目前,实际加工中主要以试切法来调整工艺参数,建立切削预测模型对生产具有重要指导意义。
张建飞[66]利用二阶响应面法建立了刀具几何参数对切削温度和切削力的预测数学模型,但参数考虑不全面。胡敏敏[92]将双重响应曲面法的二次回归模型与田口法设计的正交试验结合,求解得到了平均误差为5.82%的切削力预测模型,基于响应曲面法建立了平均误差为13.64%表面粗糙度预测模型。王晓明等[35]利用多元线性回归分析计算得出关于表面粗糙度的数学模型,并进行了显著性检验,其最大误差为8.9%。
丁宝洋等[93]在磨损机理和热力耦合条件的基础上建立正反馈模型及Simulink计算方法,并进行了刀具磨损实验,发现整体预测误差在22%以下。
刘智博[94]通过mATLAB软件将不同时刻的磨损代入经验公式中,得到相应的常数从而建立了刀具磨损预测模型,经与实验结果比较,得出误差在30%以内。ZhAoZemin等[95]将刀具寿命重新定义为表面粗糙度的函数,提出了基于时变磨损模型的刀具寿命几何分析方法用于评价刀具磨损与寿命之间的关系。
WAngZ.G.等[96]基于高速铣削的有限元模拟结果和奥克斯利理论,提出了一种新的混合切削力模型,该模型引入更复杂的刀—屑界面摩擦模型,消除了奥克斯利模型中刀—屑界面法向应力均匀分布的假设。ChenYun等[97]在正交切削预测模型的基础上,利用JohnSon⁃Cook材料模型和考虑工具热性能的热模型,将热机械效应纳入其中,建立了TC4钛合金的铣削力预测模型,但预测的铣削力波形图在相宽方面与实验结果存在差异,仍需进一步改进。
6、结语
国内外学者对钛合金切削过程进行了广泛研究,在切削参数优化、摩擦润滑、刀具参数优化、仿真技术以及新型切削技术等方面取得了诸多突破性进展,揭示了钛合金切削机理及切削规律,今后可继续以提高钛合金切削性能为目标进行更深层次的研究。
(1)在工艺参数优化方面,往往对研究对象的局限性较大,或是为了减少计算量而忽视部分因素,使研究结果的通用性较差,今后可将提高通用性为目标继续研究。
(2)在加工表面完整性研究方面,由于表面完整性的评价指标以及影响因素较多,所以对于表面完整性的分析不够充分,今后可以建立健全表面完整性评价系统。
(3)由于钛合金在低温下的优良切削性能,有必要对超低温冷却技术进行研究。
(4)为了在激光辅助加工方面实现突破,应将研究重心放在开发新型刀具以及刀具冷却方面。
(5)对于切削仿真技术方面的研究应该以提高模型精度为目标,考虑的因素应尽可能全面,优化算法,降低整体预测误差,使结果更接近实际。
参考文献
[1]胡伟楠.钛合金TC4高速切削加工性试验研究[D].沈阳:沈阳理工大学,2020.
[2]郭涛.某航空发动机钛合金整体盘轴加工工艺研究[D].大连:大连理工大学,2019.
[3]孙程成.航天钛合金件深孔高效精密加工技术[D].上海:上海交通大学,2017.
[4]续文浩.钛合金叶片型面铣削工艺优化试验与应用研究[D].上海:上海交通大学,2019.
[5]王胜,刘文军,周明安,等.PCD刀具高速铣削TC4钛合金的工艺参数优化[J].金刚石与磨料磨具工程,2020,40(4):47-52.
[6]杜红春,张祺.钛合金切削加工参数优化数学模型及工艺参数分析研究[J].机电工程,2020,37(11):1280-1287.
[7]赵云琨.钛合金金刚石精密切削表面质量研究[D].哈尔滨:哈尔滨工业大学,2013.
[8]SuiShAoChun,FengPingFA,mouWenping.TemperATuremodelingAnAlySiSFormillingoFTiTAniumAlloy[J].KeyEngi⁃neeringmATeriAlS,2016,693:928-935.
[9]杜舜尧.新型钛合金加工表面完整性与疲劳性能研究[D].南京:南京航空航天大学,2017.
[10]DuShunyAo,Chenminghe,XieLAnSheng,eTAl.OpTimizA⁃TionoFproCeSSpArAmeTerSinThehigh⁃SpeedmillingoFTiTA⁃niumAlloyTB17ForSurFACeinTegriTyByTheTAguChi⁃grey
relATionAlAnAlySiSmeThod[J].AdvAnCeSinmeChAniCAlEngineering,2016,8(10):1-12.
[11]WmerSni,mBoujelBene,SBenSAlem,eTAl.OpTimizATionoFTheSurFACeroughneSSinBAllendmillingoFTiTAniumAl⁃loyTi⁃6Al⁃4VuSingTheTAguChimeThod[J].ProCediAmAn⁃
uFACTuring,2018,20:271-276.
[12]刘杨.钛合金薄壁件腹板加工工艺参数优化[D].成都:西南交通大学,2016.
[13]杨晓勇.钛合金铣削刀具磨损及表面完整性研究[D].天津:天津大学,2013.
[14]陆涛.钛合金Ti6Al4V切削加工机理及参数优化[D].成都:西华大学,2015.
[15]陈国三.钛合金薄壁件高速铣削加工技术的研究与应用[D].南京:南京理工大学,2016.
[16]陈虹宇.面向钛合金薄壁件的铣磨加工颤振稳定性及表面质量的研究[D].沈阳:东北大学,2015.
[17]陈婷婷.钛合金薄壁腹板铣削加工变形基础研究[D].南京:南京航空航天大学,2015.
[18]章熠鑫.钛合金薄壁件加工变形控制工艺基础研究[D].南京:南京航空航天大学,2013.
[19]鲁炎鑫.硬质合金立铣刀高效铣削钛合金表面完整性研究[D].湘潭:湘潭大学,2016.
[20]罗秋生,姚倡锋,任军学.TC17钛合金高速铣削参数对表面残余应力影响研究[J].机械科学与技术,2011,30(9):1500-1503.
[21]VKriShnArAj,SSAmSudeenSAdhAm,RSindhumAThi,eTAl.ASTudyonhighSpeedendmillingoFTiTAniumAlloy[J].Pro⁃CediAEngineering,2014,97:251-257.
[22]Luoming,WAngJing,WuBAohAi,eTAl.EFFeCTSoFCuTTingpArAmeTerSonToolinSerTweArinendmillingoFTiTAniumAl⁃loyTi6A14V[J].ChineSejournAloFmeChAniCAlEngineer⁃
ing,2017,30(1):53-59.
[23]mAJiAnwei,JiAZhenyuAn,WAngFuji,eTAl.SpindleSpeedSeleCTionForhigh⁃SpeedmillingoFTiTAniumAlloyCurvedSurFACe[J].mATeriAlSAndmAnuFACTuringProCeSSeS,2014,29(3):364-369.
[24]ThomASmeurig,TurnerSAm,JACkSonmArTin.miCroSTruC⁃TurAldAmAgeduringhigh⁃SpeedmillingoFTiTAniumAlloyS[J].SCripTAmATeriAliA,2009,62(5):250-253.
[25]张一鸣.典型钛合金加工表面完整性研究[D].大连:大连理工大学,2019.
[26]侯冠明.钛合金Ti6Al4V多工步切削加工表面完整性研究[D].济南:山东大学,2019.
[27]孟龙晖.Ti6Al4V钛合金切削加工表面残余应力的研究[D].南京:南京航空航天大学,2016.
[28]孟龙.钛合金高速铣削过程建模[D].上海:上海交通大学,2013.
[29]邓小野.钛合金高速切削加工机理的仿真研究[D].沈阳:沈阳理工大学,2012.
[30]YAngDong,LiuZhAnqiAng,RenXiAoping,eTAl.HyBridmodelingwiThFiniTeelemenTAndSTATiSTiCAlmeThodSForre⁃SiduAlSTreSSprediCTioninperipherAlmillingoFTiTAniumAl⁃loyTi⁃6Al⁃4V[J].inTernATionAlJournAloFmeChAniCAlSCi⁃enCeS,2016,108-109:29-38.
[31]XinHongmin,ShiYAoyAo,ningLiqun,eTAl.ReSiduAlSTreSSAndAFFeCTedlAyerindiSCmillingoFTiTAniumAlloy[J].mATeriAlSAndmAnuFACTuringProCeSSeS,2016,31(13):1645-1653.
[32]宁晋生.面向钛合金叶片的车铣加工颤振稳定性及表面质量的研究[D].沈阳:东北大学,2018.
[33]赵伟静.钛合金零件磨切加工工艺参数及表面质量研究[D].武汉:武汉理工大学,2018.
[34]李军,任成祖,杨晓勇,等.钛合金(Ti⁃6Al⁃4V)铣削参数对表面完整性影响研究[J].机械设计,2016,33(4):1-6.
[35]王晓明,韩江.TC4钛合金高速铣削表面粗糙度研究[J].机械设计与制造,2019(5):232-236,240.
[36]周子同,崔季,陈志同,等.TB6钛合金铣削表面完整性试验研究[J].航空制造技术,2015(8):66-69,77.
[37]VKriShnArAj,BHAriKriShnA,JAmAlYSheikh⁃AhmAd.STudyoFFiniShmillingoFTiTAniumAlloy(Ti6Al4V)[J].in⁃TernATionAlJournAloFmAChiningAndmAChinABiliTyoFmA⁃
TeriAlS,2016,18(5/6):634.
[38]宋绪浩.钛合金切削加工表面质量调控研究[D].济南:山东大学,2020.
[39]何耿煌,吴明阳,李凌祥,等.典型钛合金切削层相变形成机理及其影响因素研究[J].机械工程学报,2018,54(17):133-141.
[40]孙明杰.多种钛合金铣削加工工艺研究[D].秦皇岛:燕山大学,2012.
[41]YAngPAn,YAoChAngFeng,XieShAohuA,eTAl.EFFeCToFToolorienTATiononSurFACeinTegriTyduringBAllendmillingoFTi⁃TAniumAlloyTC17[J].ProCediACiRP,2016,56:143-148.
[42]LiYu,TiAnWeijun,YAngZhenChAo,eTAl.TheeFFeCToFCuTTingpArAmeTerSonmAChinedSurFACemiCroSTruCTuredur⁃inghighSpeedmillingoFTiTAniumAlloyTC17[J].Ad⁃vAnCedmATeriAlSReSeArCh,2012,443-444:133-137.
[43]李锋,李旭东,刘维伟,等.刀具磨损对TC11铣削表面粗糙度与残余应力的影响[J].宇航材料工艺,2019,49(3):91-94.
[44]杨后川,杨保生,杜晓伟,等.钛合金TB6铣削表面粗糙度与表面缺陷研究[J].航空制造技术,2017(5):60-66,71.
[45]谢健康.TC4钛合金的深孔钻削加工系统及其刀具研究[D].西安:西安石油大学,2019.
[46]SurojiTGAnguli,ShivGKApoor.improvingTheperFormAnCeoFmillingoFTiTAniumAlloySuSingTheATomizATion⁃BASedCuTTingFluidAppliCATionSySTem[J].JournAloFmAnuFACTur⁃ingProCeSSeS,2016,23:29-36.
[47]nAoToiShii,RyuTAroTAnAkA,YuToKojimA,eTAl.inFluenCeoFCuTTingFluidonTooledgeTemperATureinendmillingoFTiTAniumAlloy[J].KeyEngineeringmATeriAlS,2015,656-657:296-301.
[48]黄丙琪.热/冷效应辅助钛合金切削的表面质量和刀具磨损试验研究[D].淄博:山东理工大学,2020.
[49]Kyung⁃HeePArk,mohdAzlAnSuhAimi,Gi⁃DongYAng,eTAl.millingoFTiTAniumAlloywiThCryogeniCCoolingAndmin⁃imumquAnTiTyluBriCATion(mQL)[J].inTernATionAlJour⁃
nAloFPreCiSionEngineeringAndmAnuFACTuring,2017,18:5-14.
[50]Kyung⁃HeePArk,Gi⁃DongYAng,mASuhAimi,eTAl.TheeFFeCToFCryogeniCCoolingAndminimumquAnTiTyluBriCATiononendmillingoFTiTAniumAlloyTi⁃6Al⁃4V[J].JournAloF
meChAniCAlSCienCeAndTeChnology,2015,29:5121-5126.
[51]刘佳佳,姜兴刚,张德远.钛合金高速旋转超声椭圆振动侧铣削切屑特征和刀具磨损研究[J].机械工程学报,2019,55(19):186-194.
[52]倪陈兵,朱立达,宁晋生,等.超声振动辅助铣削钛合金铣削力信号及切屑特征研究[J].机械工程学报,2019,55(7):207-216.
[53]邵振宇,李哲,张德远,等.钛合金旋转超声辅助钻削的钻削力和切屑研究[J].机械工程学报,2017,53(19):66-72.
[54]臧健.Ti6Al4V钛合金多工步切削加工切屑形成机理研究[D].济南:山东大学,2018.
[55]刘丽娟,吕明,武文革,等.高速铣削钛合金Ti⁃6Al⁃4V切屑形态试验研究[J].机械工程学报,2015,51(3):196-205.
[56]王来照,张子园.高速铣削钛合金Ti⁃6Al⁃4V的切屑形态分析[J].内燃机与配件,2016(9):55-59.
[57]LiAnhAi,ZhAoJun,ZhengHongguo,eTAl.ChipFormATioninhigh⁃SpeedmillingoFTiTAniumAlloywiThPCDToolS[J].mATeriAlSSCienCeForum,2014,800-801:150-154.
[58]焦锋,牛赢,赵波.难加工材料铣削残余应力研究进展[J].表面技术,2017,46(3):267-273.
[59]张翔宇,隋翯,张德远,等.高速超声振动切削钛合金可行性研究[J].机械工程学报,2017,53(19):120-127.
[60]张翔宇,路正惠,彭振龙,等.钛合金的高质高效超声振动切削加工[J].机械工程学报,2021,57(5):133-147.
[61]LiuJiAjiA,JiAngXinggAng,HAnXiong,eTAl.inFluenCeoFpArAmeTermATChingonperFormAnCeoFhigh⁃SpeedroTAryul⁃TrASoniCellipTiCAlviBrATion⁃ASSiSTedmAChiningForSidemillingoFTiTAniumAlloyS[J].TheinTernATionAlJournAloFAdvAnCedmAnuFACTuringTeChnology,2019,101:1333-1348.
[62]JiAoFeng,ZhAoLi,YAoChenglin,eTAl.ReSeArChonmill⁃ingdeFormATioninulTrASoniCviBrATionASSiSTedendmillingoFTiTAniumAlloyThin⁃wAlledpArTS[J].KeyEngineeringmATeriAlS,2018,764:174-183.
[63]王瑛.钛合金微切削过程中硬质合金刀具摩擦磨损特性研究[D].北京:北京理工大学,2017.
[64]KojiTSudA,KoiChiOkudA,HirooShizukA,eTAl.ASTudyoFThemiCro⁃endmillingoFTiTAniumAlloy[J].AdvAnCedmA⁃TeriAlSReSeArCh,2011,325:588-593.
[65]杨东.基于长疲劳寿命的钛合金Ti6Al4V铣削加工表面完整性研究[D].济南:山东大学,2017.
[66]张建飞.Ti6Al4V高速切削过程有限元模拟及切削参数优化[D].昆明:昆明理工大学,2017.
[67]RenJunxue,ZhouJinhuA,WeiJiAnwei.OpTimizATionoFCuT⁃TergeomeTriCpArAmeTerSinendmillingoFTiTAniumAlloyuSingThegrey⁃TAguChimeThod[J].AdvAnCeSinmeChAniCAlEngineering,2015:721093.
[68]徐九华,刘鹏,傅玉灿.超硬刀具高速切削钛合金研究进展[J].航空制造技术,2011(14):26-30.
[69]BAiJinxuAn,BAiQingShun,TongZhen.ExperimenTAlAndmulTiSCAlenumeriCAlinveSTigATionoFweArmeChAniSmAndCuTTingperFormAnCeoFpolyCrySTAllinediAmondToolSinmi⁃Cro⁃endmillingoFTiTAniumAlloyTi⁃6Al⁃4V[J].inTernA⁃TionAlJournAloFReFrACTorymeTAlS&HArdmATeriAlS.2018,74:40-51.
[70]姜振喜.TC4-DT钛合金切削性能研究与仿生刀具结构设计[D].济南:山东大学,2016.
[71]罗学全,于涛,蒋双双,等.TC4钛合金高速铣削加工刀具失效机理研究[J].工具技术,2019,53(9):43-46.
[72]YAngShuCAi,HeChunSheng,Zhengminli,eTAl.TemperA⁃TureFieldoFToolengAgedCuTTingzoneFormillingoFTiTAni⁃umAlloywiThBAll⁃endmilling[J].miCromAChineS,2018,9(12):672.
[73]闵令臣.钛合金高效车削刀具磨损试验研究[D].哈尔滨:哈尔滨理工大学,2014.
[74]ShiQi,LiLiAng,Hening,eTAl.ExperimenTAlSTudyinhighSpeedmillingoFTiTAniumAlloyTC21[J].TheinTernATionAlJournAloFAdvAnCedmAnuFACTuringTeChnology,2013,64(1/4):49-54.
[75]苏永生.表面织构刀具切削钛合金的基础研究[D].南京:南京航空航天大学,2015.
[76]罗胜.抛光涂层硬质合金刀片加工钛合金的切削性能试验研究[D].湘潭:湘潭大学,2017.
[77]WilmAPolini,SAndroTurCheTTA.CuTTingForCe,ToolliFeAndSurFACeinTegriTyinmillingoFTiTAniumAlloyTi⁃6Al⁃4VwiThCoATedCArBideToolS[J].ProCeedingSoFTheinSTiTuTionoFmeChAniCAlEngineerS,PArTB:JournAloFEngineeringmAn⁃uFACTure,2016,230:694-700.
[78]JunSukeFujiwArA,TAkAAkiArimoTo,KAzuyATAnAkA.HighSpeedmillingoFTiTAniumAlloy[J].AdvAnCedmATeriAlSRe⁃SeArCh,2011,325:387-392.
[79]OgAnyAnmAkSim,VereSChAkAAlexey,VoloSovAmArinA,eTAl.inFluenCeoFTheAppliCATionoFweAr⁃reSiSTAnTCoATingSonForCepArAmeTerSoFTheCuTTingproCeSSAndTheToolliFedur⁃ingendmillingoFTiTAniumAlloyS[J].mATeriAlSTodAy:Pro⁃CeedingS,2021,38:1428-1432.
[80]SuHonghuA,LiuPeng,FuYuCAn,eTAl.ToolliFeAndSur⁃FACeinTegriTyinhigh⁃SpeedmillingoFTiTAniumAlloyTA15wiThPCD/PCBnToolS[J].ChineSeJournAloFAeronAuTiCS,
2012,25(5):784-790.
[81]林凤添.硬质合金高温性能对TC4钛合金高速铣削的影响研究[J].工具技术,2020,54(12):35-38.
[82]mATThewSDArguSCh,ThArmAlingAmSivArupAn,miChAelBerminghAm,eTAl.ChAllengeSinlASer⁃ASSiSTedmillingoFTiTAniumAlloyS[J].inTernATionAlJournAloFExTrememAnu⁃
FACTuring,2021,3(1):71-84.
[83]唐柏清.钛合金车削加工刀具磨损建模技术研究及预测分析[D].西安:西安理工大学,2019.
[84]孙玉晶,孙杰,李剑峰.钛合金铣削加工刀具磨损有限元预测分析[J].机械工程学报,2016,52(5):193-201.
[85]张富君.高速切削钛合金刀具磨损仿真的研究[D].沈阳:沈阳理工大学,2016.
[86]钱丽丽.钛合金薄壁件加工工艺分析与变形预测研究[D].南京:南京航空航天大学,2013.
[87]周培培.钛合金切削振动特性及对表面粗糙度影响的研究[D].沈阳:沈阳理工大学,2017.
[88]HuAngShuTAo,ChenWAnyong,ZhouLi.FiniTeelemenTSimulATionreSeArChonAlArgeCuTTingdepThAndquASi⁃highSpeedS3DmillingoFTiTAniumAlloyS[J].mATeriAlSSCienCe
Forum,2014,800-801:269-274.
[89]LinYouxi,YAnCongming.Three⁃dimenSionAlFiniTeelemenTAnAlySiSinCuTTingTemperATureForhighSpeedmillingoFTi⁃TAniumAlloyS[J].AdvAnCedmATeriAlSReSeArCh,2011,189-193:2259-2263.
[90]WAngZhendA,ZeXiAngBo,YouSuFYuSuFABudllAhi,eTAl.Three⁃dimenSionAlFiniTeelemenTSimulATionoFhighSpeedmillingoFTiTAniumAlloyTi6Al4V[J].JournAloFPhySiCS:ConFerenCeSerieS,2021,1948(1):012130.
[91]武永甫.航空铝合金高速铣削表面残余应力预测与实验研究[D].上海:上海交通大学,2013.
[92]胡敏敏.钛合金TC4高速铣削试验研究及数值模拟[D].昆明:昆明理工大学,2016.
[93]丁宝洋,白倩,刘具龙,等.基于Simulink反馈方法的钛合金铣削刀具磨损预测[J].机械工程学报,2019,55(11):224-232.
[94]刘智博.基于有限元仿真的钛合金铣削用刀具切削性能评价[D].哈尔滨:哈尔滨理工大学,2021.
[95]ZhAoZemin,LiuXiAnli,YueCAixu,eTAl.ToolquAliTyliFeduringBAllendmillingoFTiTAniumAlloyBASedonToolweArAndSurFACeroughneSSmodelS[J].AppliedSCienCeS,2020,10(9):3316.
[96]WAngZG,mRAhmAn,YSWong,eTAl.AHyBridCuTTingForCemodelForhigh⁃SpeedmillingoFTiTAniumAlloyS[J].CiRPAnnAlS:mAnuFACTuringTeChnology,2005,54(1):71
-74.
[97]ChenYun,LiHuAizhong,WAngJun.PrediCTivemodellingoFCuTTingForCeSinendmillingoFTiTAniumAlloyTi6Al4V[J].ProCeedingSoFTheinSTiTuTionoFmeChAniCAlEngi⁃
neerS,PArTB:JournAloFEngineeringmAnuFACTure,2018,232(9):1523-1534.
第一作者:周知进,博士,教授,广西科技大学机械与汽车工程学院,545006广西壮族自治区柳州市
FirSTAuThor:ZhouZhijin,Ph.D.,ProFeSSor,SchooloFme⁃chAnicAlAndAuTomoTiveEngineering,GuAngxiUniverSiTyoFSci⁃enceAndTechnology,Liuzhou,GuAngxi545006,ChinA
相关链接